Как выполнить соосную расточку отверстий расположенных на двух противоположных стенках корпуса, при невозможности выполнения обработки за одну установку?
Для обеспечения требуемой точности взаимного положения отверстий, расположенных на противоположных сторонах корпусной детали, нужно выполнять расточку этих отверстий с одной стороны и за одну установку. Однако иногда по разным технологическим причинам обработку отверстий приходиться выполнять с двух сторон корпуса. В этом случае для получения заданной соосности отверстий необходимо придерживаться определенной технологии, которая подробно описана ниже на конкретном примере. Пример. На рисунке 1 изображен эскиз корпуса, у которого на двух боковых стенках расположено по два соосных отверстия (Ø200 и Ø160).
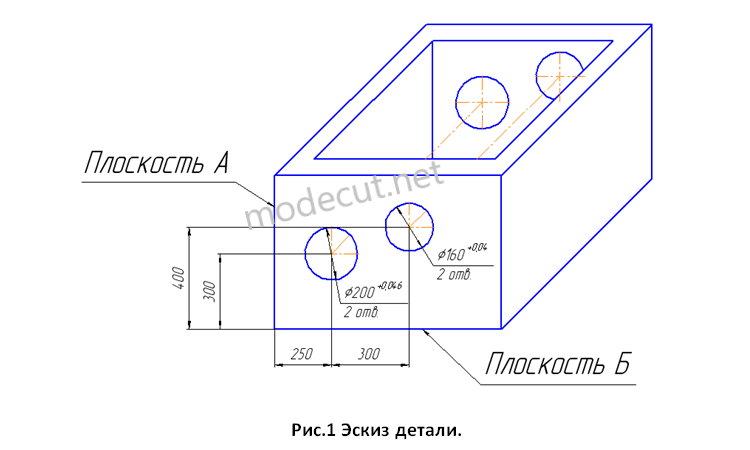
Сначала необходимо произвести обработку базовой плоскости Б, на которую будет установлен корпус при последующей расточке отверстий (см. рис.1). Устанавливаем корпус на боковую поверхность, выставляем по плоскости и фрезеруем плоскость Б (рис.2 установка 1). После обработки переустанавливаем корпус на поверхность Б. Необходимо корпус ставить не прямо на стол станка, а на шлифованные в один размер опоры. Такая установка обеспечивает свободный выход фрезы при фрезеровке боковых стенок корпуса. Выставляем по плоскости и фрезеруем боковую стенку корпуса, которая будет базовой поверхностью (плоскость А) при нахождении центра отверстий (установка 2 переход 1(рис.2)).
После обработки боковой поверхности (плоскость А) поворачиваем стол на 900. При необходимости проверяем точность поворота стола станка по этой же базовой плоскости А.
Далее определяем координаты положения шпинделя станка относительно обрабатываемого корпуса. Определение текущего положения выполняется с помощью контрольной оправки, которая крепится в шпинделе станка. Для нахождения центра шпинделя по вертикали бабка опускается на стол станка до тех пор, пока между столом и контрольной оправкой плотно будет заходить концевая мера, какой либо определенной толщины (S) (см. рис.3). При этом концевая мера большей толщины в полученный зазор заходить не должна. Текущее расстояние от плоскости стола до центра шпинделя рассчитывается по следующей формуле:
где d – диаметр контрольной оправки (мм), S – толщина концевой меры (мм). Расстояние по вертикали от текущего положения центра шпинделя станка до центра обрабатываемого отверстия корпуса (Ø200) определяем следующим образом:
где H – высота опор, на которых установлен корпус (мм), 300 мм – текущее расстояние от основания до центра отверстия Ø200 (см. рис.1), Y – текущая координата центра шпинделя по вертикали.