Как просверлить ровное отверстие в тонкостенной детали?
Довольно часто в результате сверления тонкостенной детали стандартно заточенным сверлом получается отверстие некруглой, обычно пятигранной формы. Этот дефект возникает из-за потери центрирования инструмента в процессе сверления (см. рис.1). Дело в том, что режущая часть сверла имеет два центрирующих элемента. Это центральная перемычка и боковые кромки, расположенные на ленточках сверла. В случае если высота режущей части спирального сверла “h” больше толщины детали “S”, то в момент выхода перемычки из материала, боковые кромки ещё не врезаются в заготовку и не могут центрировать сверло (см. рис.1). В результате чего и получается некруглое отверстие.
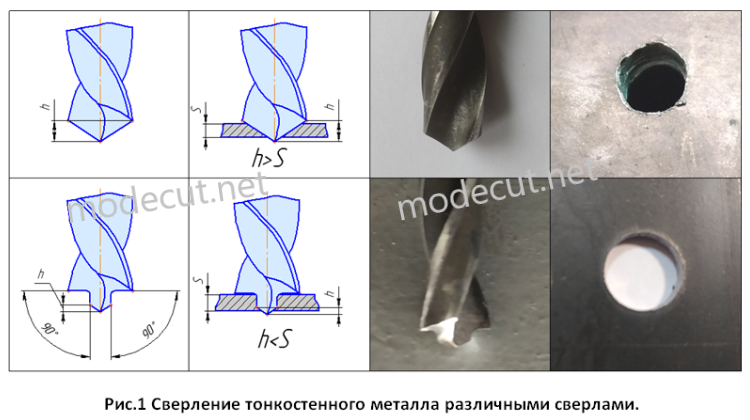
Чтобы просверлить ровное отверстие нужно переточить сверло таким образом, чтобы на нем были сформированы внешние режущие кромки, расположенные под углом 900 относительно оси вращения сверла (см. рис.1). При этом центральная режущая часть сверла (примерно 1/3 диаметра) остается неизменной, а её высота становиться меньше толщины заготовки. В момент выхода перемычки из зоны резания сверло не теряет центрирования благодаря дополнительным боковым кромкам, полученным в процессе заточки.
Для выполнения такой заточки необходимо, чтобы торец абразивного круга был заостренным, а спиральное сверло изначально было правильно заточено. Перед заточкой на подручник заточного станка устанавливается упор (в виде уголка), так чтобы его боковая сторона была перпендикулярна периферии абразивного круга и находилась примерно на расстоянии 1/3 диаметра сверла от его торца (см. рис.2). Выставляем упор на требуемое расстояние и прижимаем его струбциной к подручнику.
Во время затачивания сверло удерживается двумя руками. Первая рука удерживает сверло за направляющую часть и прижимает его к упору. Вторая рука удерживает сверло за хвостовик. Сверло прямолинейно (вдоль упора) подводиться к абразивному кругу и касается его кромки. При этом сверло должно находиться в горизонтальном положении (см. рис.3).