Какая резка лучше: газово-плазменная,
лазерная или гидроабразивная?
Вопрос выбора способа резки деталей из листового проката, часто возникает на стадиях разработки новых технологий и планирования производства. Сразу стоит отметить, что все технологические способы резки имеют свои преимущества и недостатки. Поэтому для правильного выбора необходимо провести детальный анализ условий производства по трем основным показателям: обрабатываемости, технологическим параметрам и экономическим критериям. Обрабатываемость характеризуется свойствами разрезаемого материала и толщиной заготовки. Ниже в таблице приведены данные по резке материалов разными технологическими способами, а также указана максимальная толщина разрезаемой заготовки.
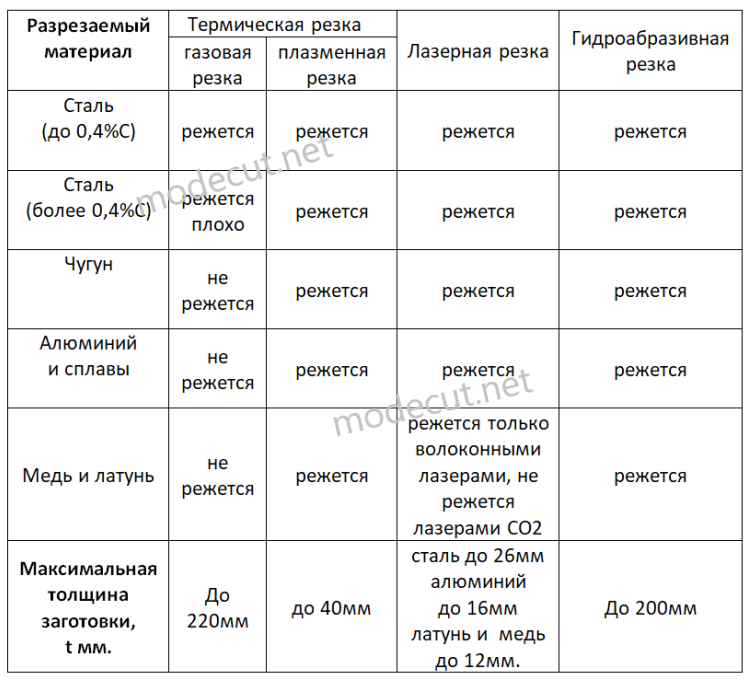
Из приведенной таблицы видно, что только газовая резка имеет большое количество ограничений по обрабатываемым материалам, так как процесс основан на сгорании металла в струе кислорода. Однако современные машины термической резки, кроме газового резака оснащены устройством плазменной резки, которое может резать остальные виды металлов и сплавов. Также из таблицы видно, что не все виды лазеров могут резать медь и латунь. Это связано с тем, что лазеры СО2 генерируют инфракрасное излучение с длиной волны 9,4-10,6мкм, которое полностью отражается от поверхности медных и латунных заготовок. Стоит отметить, что с помощью лазерной и гидроабразивной резки можно разрезать не металлические материалы (дерево, ткань, пластмассы и т.д.).
По толщине разрезаемой заготовки лазерная (до 26мм) и плазменная резка (до 40мм) имеют серьёзные ограничения. Эти ограничения связаны с лимитированной мощностью источников питания. Плазменная резка выполняется плазменной струей, которая создается от электрической дуги между электродом и деталью. Чем толще заготовка, тем больше сопротивление и тем больше должна быть мощность источника. При лазерной резке мощность резания тоже зависит от источника питания. Чем мощнее источник питания, тем больше толщина разрезаемой заготовки.
Технологические параметры характеризуются скоростью и качеством срезанной кромки. В приведенной далее таблице показаны рекомендуемые скорости резания разных способов резки в зависимости от толщины обрабатываемой заготовки, а также описано качество реза, полученного после каждого способа обработки.
По табличным значениям видно, что наибольшей скоростью резания обладает лазерная резка. Однако при увеличении толщины заготовки скорость резания лазерной резки значительно снижается. Считается, что лазер является наиболее эффективным способом резки заготовок толщиной до 6мм. Также стоит отметить, что скорость лазерной резки сильно зависит от мощности источника. Чем больше мощность, тем выше скорость резания. Для наглядности в таблице приведены несколько значений скорости резания (при лазерном источнике на 2 кВт и 6кВт).
Плазменная резка также имеет довольно высокую скорость резания и считается самым эффективным способом при разрезании заготовок толщиной от 6 и до 30мм. Самую низкую скорость резания имеет гидроабразивная резка, но по качеству резки этот способ занимает самые лидирующие позиции. Полученный рез имеет минимальную конусность и высокую точность обработки. Высокое качество реза имеет и лазерная резка. В ряде случаев детали полученные данными способами не требуют дополнительной механической обработки. При плазменной резке качество образованной кромки заметно ниже, а газовая резка имеет самые худшие показатели.